What Is a Tesla Car Battery Made of
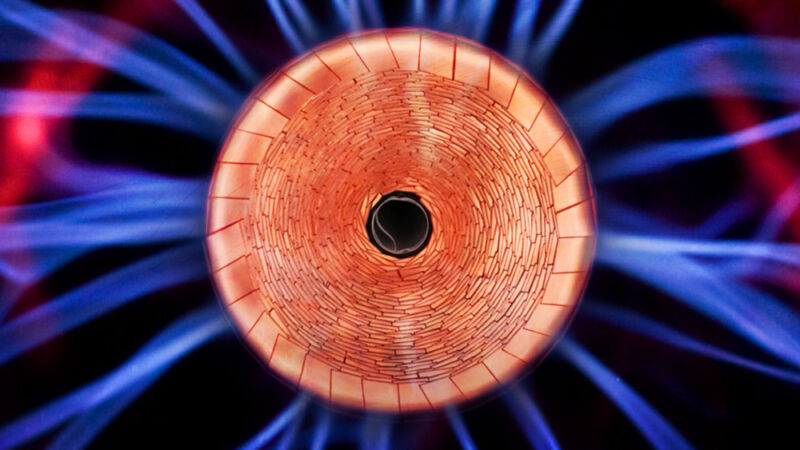
Enlarge / Gaze upon Tesla's new battery cell, but don't despair.
Aurich Lawson / Tesla / Getty Images
Tesla's "battery day" Tuesday revealed a surprising amount of information about projects the company has kept under wraps. The presentation described changes and improvements to just about every aspect of its battery packs, with big-picture implications for the claim that a $25,000 Tesla vehicle would be possible in about three years. (See the previous coverage from Ars' Timothy Lee for more on that.) But it wouldn't be a Tesla announcement without vague timelines, and it was a little unclear which improvements are ready to go now—and which ones they're just expecting to succeed in the next couple of years.
Without specific numbers or concrete details, assessing the announcements takes a little guesswork. But we can compare all this to other industry trends and to published research to get some idea.
Battery in a can
Let's start with two things Tesla claimed already exist at its pilot production plant: its new cell design and some improvements in manufacturing. Tesla got off the ground using existing and commonly available cylindrical 18650 lithium-ion cells, while most EVs have been built with flat pouch or prismatic cells (more like the thin batteries in phones and laptops). In a cylindrical cell, long sheet-like anodes, separators, and cathodes are sandwiched, rolled up, and packed into a cylinder-shaped can. The cathode and anode sheets each have one skinny "tab" that connects to the positive and negative terminals of the battery can.
One of the best ways to make a battery more energy dense is to get rid of as much packaging as possible. Make the separator super thin and minimize the space-eating outer container and battery pack components, and you've got more electricity stored per kilogram. Obviously there are limits to how much you can shave off, so another way of doing this is increasing the ratio of battery volume to packaging area. That is, make a bigger can.
Tesla did this when it introduced the 2170 cell with the Model 3 and Powerwall. This cylinder was 21 millimeters by 70 millimeters rather than the 18 by 65 dimensions of the 18650 cell. But going bigger presented Tesla with challenges because a bigger can holds longer rolls, and longer rolls mean the anode and cathode stretch out farther from the tab connecting them to the battery terminals. The longer path for electrons causes problems for safe rapid charging and creates more heat that has a harder time escaping.
Tesla's solution to this, leading to a much larger 4680 cell, is a new "tabless" design with contacts running the length of the anode and cathode sheets—forming a rose-like gathering at the ends when everything is rolled up—keeping the electrical path length to the terminal short throughout the sheet. "Sometimes, what's elegant and simple is still hard," Tesla's Drew Baglino said. "And it took us a lot of trials, but we're happy where we ended up."
"It may sort of sound a bit silly to some people," Musk added, "[but] for people that really know cells, this is a massive breakthrough."
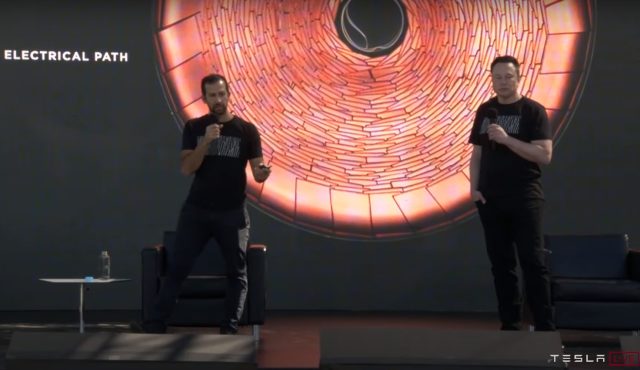
Enlarge / Elon Musk and Drew Baglino present in front of a slide showing Tesla's new "tabless" cell design.
Tesla
It's genuinely hard to know precisely how this stacks up with cells used in other EVs, given how secretive manufacturers are, but it could be that this tabless design validates Tesla's choice to stick with the cylindrical cell shape.
The other half of making a new kind of cell is designing the machines that do the making. As detailed in our companion story, Tesla has found ways to substantially increase the throughput of portions of the battery line. The tabless design actually helps with this, as the electrode sheet can just keep flying through the rollers. And together with other changes we'll get into in a moment, they're talking about increasing production while using less factory floorspace and less energy. That will help them reach cost reduction goals and ramping output goals.
Pack it up, pack it in
An EV doesn't run on a battery cell, of course, but rather a battery pack full of cells. There's a lot going on in these battery packs, including charge management, cooling, and safety measures in case of fire. That makes the engineering of the pack very much relevant to the overall energy density of the vehicle's storage, and therefore its range.
Tesla described a new pack design that reduces some of the structural supports, which means more cells in less volume. And as this involves a redesigned pack that doubles as structure for the vehicle, it probably carries some cost benefits at the vehicle level, as well.
This pack design presumably exists, but there was no word on which vehicles it will go into. Might production switch over on an existing vehicle, or is this design simply part of the Cybertruck, Tesla Semi, or unnamed $25,000 vehicle? Musk didn't say.
But he did have a lot to say about the chemistry inside the new battery cells. And this is where the timelines get hazier. New chemistries for both the anode and cathode were discussed—both would break new ground.
The anode in modern lithium-ion batteries is graphite. The structure of graphite allows it to host the lithium atoms that move toward the anode during charging, but that's all it does. This means that a substantial portion of the cell's volume and weight doesn't directly contribute to energy storage beyond simply keeping the thing working. If you could ditch some volume and weight there, the energy density of the cell would increase.
Tesla and some other manufacturers currently add a bit of silicon inside that graphite, as this enables the same volume of anode to hold more lithium. A significantly better (and cheaper) option would be the use of pure silicon. But while graphite allows lithium in and out without changing shape, silicon has a nasty habit of expanding as it loads up with lithium. That creates structural failures within the silicon, degrading performance over time, and potentially dangerous failures of the cell container.
There's a lot of research on alternative anodes for lithium-ion batteries, but none has quite reached the market. Tesla claims to have designed an anode with tiny silicon particles in a conducting, elastic polymer. That allows for a long-lived and safe silicon anode cell, it says—which would be a big deal.
This cell comes with a claimed cost decrease from about $10 per kilowatt-hour for silicon-in-graphite to more like $1 per kilowatt-hour for pure silicon. As for vehicle range, the company claims a 20-percent improvement. But no other properties (like longevity compared to its current anode) were described, so it's unclear whether Tesla is ready to put this in a battery and sell it today. (Though for what it's worth, it doesn't sound too different from an anode material Sila Nano—a company with some Tesla alumni—says it'll start providing for electronic device batteries this year.)
Tesla is also moving to (slightly) different chemistries on the cathode side. And yes, that's plural chemistries, which is at least as noteworthy as the nitty-gritty chemical details. Tesla now wants to provide three different types of lithium-ion batteries, ranging from more economical to I'm-giving-her-all-she's-got-captain.

Enlarge / Here's how Tesla presented its plan to use three different cathode chemistries for different applications.
Tesla
Tesla currently uses an NCA chemistry (that's lithium-nickel-cobalt-aluminum), while lithium-nickel-manganese-cobalt (NMC) chemistries are common across the rest of the EV industry. Cobalt is the most expensive of these elements, and most of it is sourced from mines in the Democratic Republic of the Congo, where unsafe working conditions and child labor are serious problems. As a result, the industry has been trying to reduce cobalt usage.
What Is a Tesla Car Battery Made of
Source: https://arstechnica.com/cars/2020/09/heres-what-tesla-will-put-in-its-new-batteries/
0 Response to "What Is a Tesla Car Battery Made of"
Post a Comment